Investment Casting
Why choose the Investment Casting process?
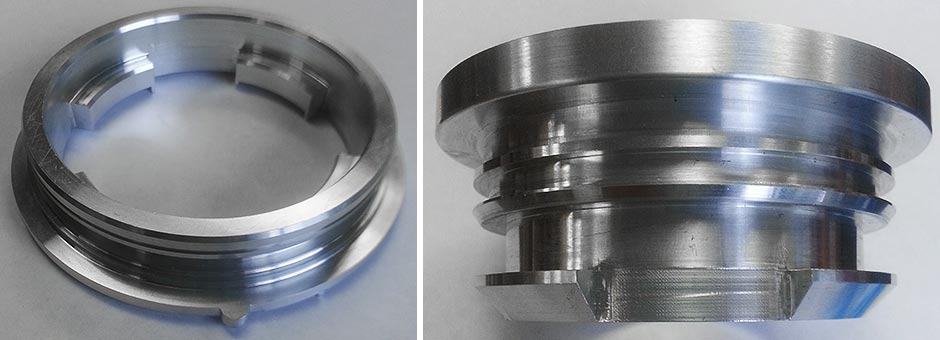
One of the oldest known metal-forming techniques, investment casting or lost wax process casting is a complex and multi-step cast manufacturing process. An initial wax pattern of the part to be cast is coated with a ceramic refractory material and fired. The wax is then melted out to leave a ceramic cavity, into which the molten metal or alloy is poured. Upon cooling, the metal solidifies and the ceramic mold is broken out, leaving behind an exact duplicate of the desired part.
Investment casting enables the fabrication of near-net-shaped metal parts with complex geometries and intricate details, from almost any alloy.
In addition, parts that are investment-cast have excellent surface finishes and require very little secondary machining; they also allow for tighter dimensional tolerances (typically, a linear tolerance of ±0.004 inches is standard).
Investment casting is therefore used in the manufacture of extremely complex parts that use specialized alloys or need a lot of machining, and/or which cannot be produced by traditional methods. Although investment casting is more expensive than other comparable casting techniques, the expense is offset by savings in material, labor and finishing.