Custom Screw Machine Part Tolerances Explained
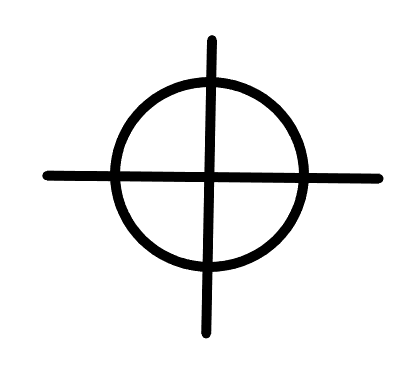
The significance of part tolerances can’t be overstated. These critical measurements ensure components fit flawlessly into complex assemblies, maintaining the functionality and safety of the final products.
Tolerance is especially important in the automotive, electronics, and aerospace sectors, where even one minor deviation can lead to catastrophic failures or costly recalls.
One way to ensure part tolerances are met is through screw machining. In this blog, we’ll explore the role that screw machining plays in maintaining these stringent standards.
Screw machining is known for its ability to achieve exceptionally high tolerances. The standard in screw machining and any method used to create precision components is +/- 0.005.” However, some advanced setups that incorporate CNC technology can achieve even tighter precision. CNC technology supports tolerances as fine as +/- 0.0001.”
The specific tolerance limits can vary based on factors such as the material used, part complexity, and the specific type of screw machine used. In the sections below, we’ll discuss how some of these factors influence tolerances.
The application environment is the most significant factor influencing the tolerances required for screw-machined parts like bushings, spacers, and connectors.
Parts exposed to temperature extremes must accommodate thermal expansion and contraction. Tighter tolerances help reduce the risk of fitment issues or mechanical failures.
Similarly, components subjected to high mechanical stress must have tolerances that allow them to maintain integrity under load without compromising their functionality.
Part size also plays a critical role in determining the tolerances achievable through screw machining. Smaller components often require tighter tolerances because minor deviations can significantly impact their function and fit within an assembly. Conversely, larger parts may accommodate slightly looser tolerances due to their size and the relative impact of variations.
However, the precision level still needs to be adjusted based on the part’s specific function and the precision required for it to operate effectively within its mechanical system.
More intricate designs, with features like thin walls, complex curves, or tight clearances, require stricter tolerances to ensure the part functions as intended. For example, angular tolerances in machining can range from +/- 0.5 degrees for less critical applications to as precise as +/- 0.1 degrees for high-precision needs.
Engineers must carefully balance the design complexity with achievable tolerances, ensuring that the parts are manufacturable while meeting functional and operational requirements.
The material used in screw machining also influences the achievable tolerances due to each material’s properties.
Metals like brass and aluminum are generally more malleable, allowing for tighter tolerances and easier machining. Brass, for instance, can often be machined to tolerances as tight as +/- 0.0005” due to its softness and ductility. Aluminum, while slightly harder, still maintains high machinability with similar tolerances.
Stainless steel, being harder and more abrasive, often requires slightly looser tolerances, typically around +/- 0.001,” as it is more demanding on machining tools and can wear them down faster.
Conversely, polymers like nylon and PEEK behave differently than metals. These materials are softer and more prone to deformation under machining stress, thermal expansion, and moisture absorption. This variability can affect the precision of the final product, often requiring looser tolerances compared to metals. Tolerances for polymers might range from +/- 0.002 to +/- 0.010,” depending on the specific conditions of the machining process and the part’s application requirements.
Lastly, the chosen machining method and the conditions under which machining takes place will influence achievable tolerances.
For example, traditional screw machining might offer different precision capabilities compared to CNC machining, which provides greater control over cutting speeds, tool movements, and more complex part geometries. Additionally, machining conditions such as tool wear, machine stability, and the presence of lubricants can impact the quality of the finished product. Tool wear can lead to less precise cuts, while machine instability and inadequate lubrication impact accuracy and surface finish, directly affecting the tolerances.
Founded in 1995, AmTech is a specialty manufacturer helping Tier I and Tier II suppliers worldwide. Our capabilities include single- and multi-spindle CNC Swiss screw machining, investment casting, custom shaft manufacturing, prototyping, forging, and more. We can manufacture screw-machined parts up to 24” in length and 3” in diameter and can achieve tolerances within +/-.001.″ We also offer a just-in-time delivery program for customers in the United States, Mexico, Canada, and Western Europe.
Please contact us today to learn more about our screw machining capabilities or visit our blog for more resources.