Case Study: Redesign To Reduce Production Cost
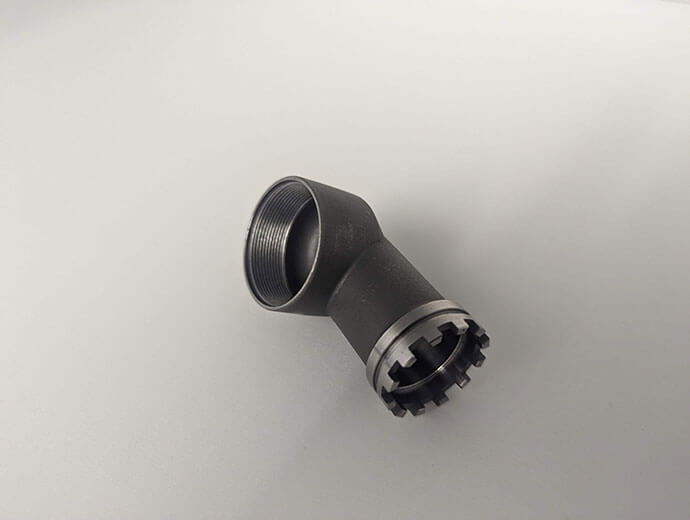
The original design of the shafts was a single piece spline shaft, with the splines cut via a pinion cutting process. AmTech suggested a two-piece design, with the front end splined by broaching, a less expensive process than pinion cutting. One key factor to help reduce production costs.
Broaching is especially good for odd shapes like keyways, non-circular holes and in this case splines. Because broaching is performed in a single pass it is extremely efficient and is ideal for high volume applications. Secondly, rather than using press fit or threading to fasten the mating parts of the shaft, we suggested using the shrink-fitting process to achieve the same result at a lower cost. The enveloping female part was heated in a furnace and the enveloped male part was cooled by freezing.
A robotic fixture then assembled the two parts into position immediately, and the shaft was allowed to cool to room temperature, resulting in a strong locked interference of both parts. The shrink-fitting process has many benefits: process control, consistency, accuracy and speed. These benefits are what make this operation repeatable and accurate for high volume applications.
AmTech’s team was able to draw on more than 25 years of design and engineering experience to deliver an improved shaft design that yields a 35 percent cost reduction for the entire assembly. While still meeting drawing specifications and providing a consistent product in high volume production runs.