How Bevel Gears Are Made?
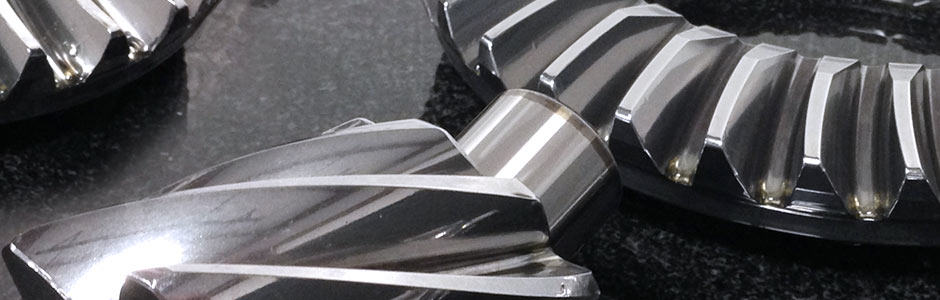
Bevel gears are gears designed to transmit motion between intersecting axes. The important features of these gears are that the tooth-bearing surfaces are conical, and that the axes of the two shafts intersect. Bevel gears are typically mounted on shafts that are 90 degrees apart, and are therefore mainly used to change the operating angle and thereby the direction of rotation by 90 degrees; however, they can be designed to work at other angles as well.
Depending on their geometry, bevel gears, may be classified as straight, spiral, zerol and hypoid.
In addition to their ability to transfer power and motion across non-intersecting shafts, bevel gears offer high efficiency (98% or higher), and are not very noisy during operation.
Force output and power can be easily manipulated by changing the number of teeth, thus allowing a relatively weaker source of power to potentially generate a much stronger output of energy.
To function optimally, bevel gears must be precisely mounted, and the shafts’ bearings must be capable of supporting significant forces.
Due to their ability to change the direction of force and the operating angle of the machinery, bevel gears are used in many diverse applications such as locomotives, marine applications, automobiles, printing presses, cooling towers, power plants, steel plants, railway track inspection machines, etc.
One of the most common uses is in the hand drill, where bevel gears change the vertical rotation of the hand into the horizontal rotation of the drill. Another well-known use is in differential drives of motor vehicles, where bevel gears enable the transmission of power to two axles spinning at different speeds, such as those on a cornering automobile.
Helicopter engines utilize bevel gears to redirect the shaft of the engine to the vertical turn of the rotors. These gears are also used in the functioning of mechanical garage doors.