What is Magnetic Particle Inspection?
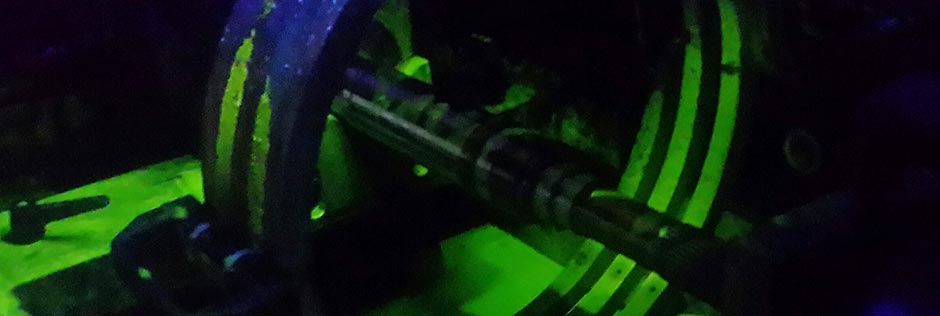
The Magnetic Particle Inspection is a nondestructive testing method to detect defects (example: material cracks) in precision components. This inspection process is quick and simple to complete and surface prep is not as critical for NPI as it is for some other testing methods.
By using tiny magnetic particle elements and magnetic fields, Magnetic Particle Inspection, to detect the part defects or cracks. Since the parts have to be magnetized for Magnetic Particle Inspection to work, this type of NDT method will only work on Iron, Steel and other ferromagnetic material alloys. Engineered parts such as housings, shafts and assemblies receive this type of nondestructive testing. The most common industries to use MPI includes: Automotive, Aerospace, Agricultural, Off-Highway, Defense and Power Generation OEMs.
The MPI method has several testing options:
In most instances, all loads are maximum on the surface of a component and they decrease inside the part.
For example, When inspecting the pictured drive shaft for a crack – the surface of the shaft has double the weakness of the inside of the shaft. The result is the fact that maximum operational force will greatly affect the surface, since it is the weakest section of this product.
One of the best advantages that a MPI provides, rather than some of the other nondestructive inspection options, is that flaw detections commonly depict the actual imperfection. This great benefit does not exist with other methods – Ultrasonic or ECI – where electronic signals need to be analyzed and results output from a machine. Instead, when MP inspection is used the surface cracks on the shaft would appear as clear and defined lines to illuminate the entire crack running through the material.
This advantage shows why MPI is the best method for efficient human inspection.