How Die Casting Reduced Servo Component Costs by 45% Efficiently
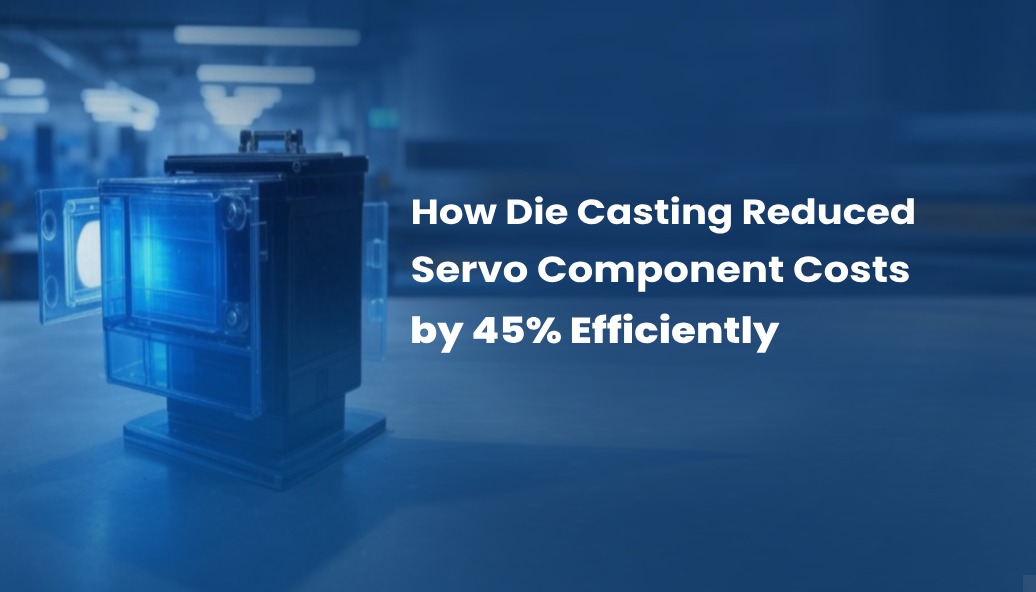
A highly specialized precision component used in a fluid fitting for a servo sensor was provided to AmTech for a manufacturability study.
An EV sales team submitted the RFQ to our design engineers. To understand the pain points, our design team engaged directly with our engineering team — and what we discovered was eye-opening.
The original manufacturing process was as follows:
This approach, while effective in terms of quality, created three major challenges:
Because this component became a bottleneck in the company’s rapidly scaling production, they needed a more scalable, cost-effective solution.
The original process involved:
We consulted with our manufacturing engineers in India to explore a better solution. The turning point came when we proposed creating a lost wax mold with sliding inserts intersecting at 90 degrees for quick sample production— and everything changed.
We quickly developed the mold, produced 50 sample parts, and validated that the component could be manufactured using precision high-pressure die casting.
After reviewing the geometry, load conditions, and material requirements, our team proposed a new approach:
Precision high-pressure aluminum die casting with minimal finish machining.
Key Improvements:
By shifting to die casting, we helped the company achieve:
This was not just a cost-cutting initiative — it was a manufacturing breakthrough that scaled seamlessly with company’s growth.
To make the die-cast solution successful, we:
All performance and compliance standards were fully met, including:
At AmTech International, we believe the biggest wins often come from rethinking the smallest components. By transforming the end fitting from fully-machined to precision-cast, we delivered:
This is what we mean by “Innovative Solutions in Motion.”
✅ Customer Reaction & Outcome
We presented the samples to client — and they were blown away. The parts passed assembly and functional testing, and Amtech was ultimately awarded the full production contract.