Case Study
Case Study: Electric Door Parts Created through Investment Casting
Challenge:
The customer initially manufactured the electric door part using bar stock, involving intricate Gang milling process resulting in escalated production costs as well as down town to load and unload fixtures.
The tolerance of the slot were very tight. We had a zoom meeting with customer and our focus was to explore if the tolerance of the slots can be 0.004 inches . Customer was not open to do so due the mating parts was also a close tolerance cylinder.
Solution:
Our enginerring team visited customer to understand how the complete mechanism operated. Finally we made the subject parts as well the mating cylinder via investment casting so the tolerance stack was functioning better then parts made machining methods.
Results:
The shift to Investment Casting realized a notable 30% cost savings. The intricate slots required for the electric door part were efficiently produced, significantly enhancing the overall efficiency of the manufacturing process.
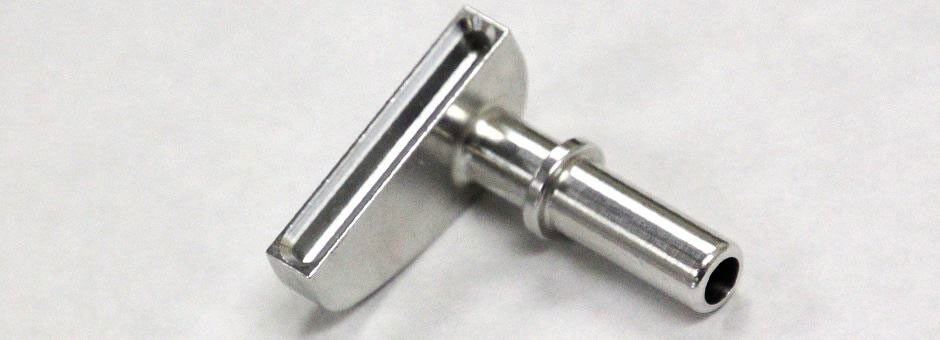
Conclusion:
AmTech’s strategic pivot to Investment Casting not only substantively reduced production costs but also streamlined the manufacturing process for the electric door part, showcasing our commitment to innovative and cost-effective solutions.