Balancing Stockpiling and Diversification: Lessons from the 2018 Trade War
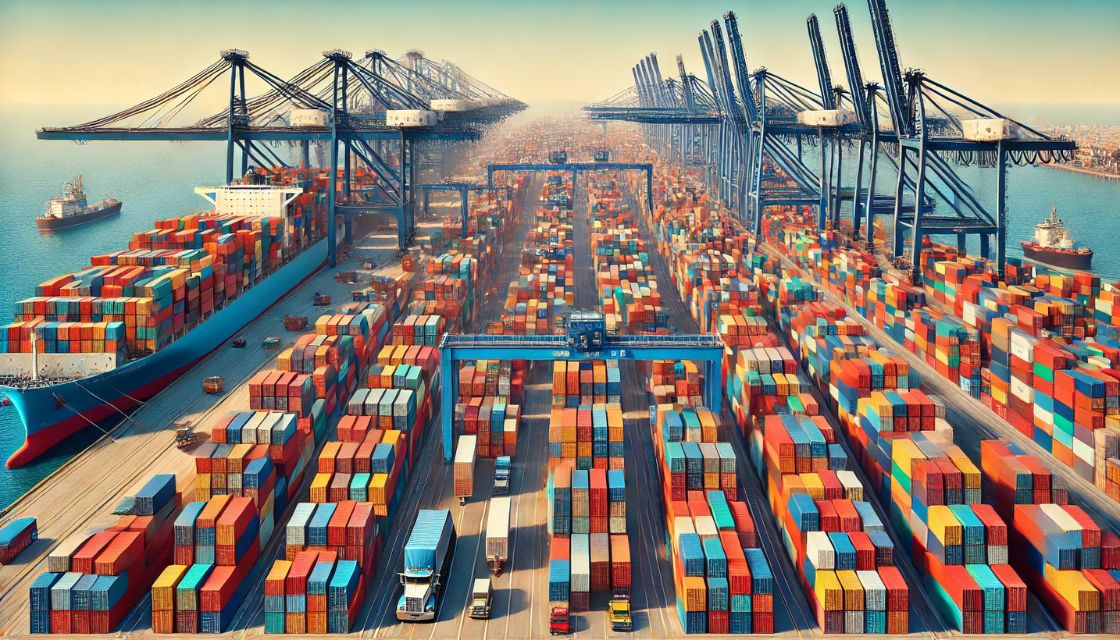
With President Trump returning to office and announcing new tariffs on Chinese imports, U.S. importers are already stockpiling goods to prepare for the anticipated trade disruptions. This surge in activity mirrors the strategies employed during the 2018–2019 trade war in Trump’s first term. Reflecting on how stockpiling played out then offers valuable insights for manufacturers navigating today’s challenges.
While stockpiling provided short-term relief during the last trade war—helping businesses avoid immediate cost increases and keep production running—it also exposed significant downsides that manufacturers must carefully evaluate.
For some industries, stockpiling during the 2018 trade war delivered tangible benefits. Automotive manufacturers secured key materials like aluminum and steel ahead of tariffs, sidestepping price surges that hit competitors who delayed action. Similarly, electronics companies stockpiled semiconductors and components, ensuring they could meet demand without passing higher costs onto consumers.
Data underscores how widespread this strategy became. In 2017, as trade tensions mounted, U.S. aluminum imports surged by 18% in the first ten months compared to the same period the previous year, according to the U.S. Department of Commerce. Semiconductor imports from China followed a similar pattern. According to S&P Global, imports jumped by 44.3% in the three months leading up to October 2018 as suppliers rushed to beat the tariffs. However, this was followed by a steep drop—falling 38.7% in October 2018 compared to the same month in 2017—highlighting how excess inventory quickly accumulated.
Consumer goods manufacturers also benefited. Companies reliant on Chinese imports for items like appliances and home electronics used stockpiling to stabilize prices and avoid supply chain disruptions. For these businesses, stockpiling provided a crucial buffer, helping them weather the initial wave of tariffs.
The benefits of stockpiling were built on a key assumption: that trade tensions would be short-lived. Few predicted that tariffs would persist across administrations, becoming a bipartisan tool in U.S. trade policy. Today, tariffs are no longer temporary disruptions but long-term realities manufacturers must plan for.
Under the Biden administration, the tariffs were retained and even expanded, with a focus on supporting key domestic industries through targeted exclusions. Tariffs were raised on critical imports like electric vehicles, solar cells, and steel and aluminum products to counter what the administration deemed unfair trade practices by China.
Now, with Trump back in office and announcing an additional 10% tariff on Chinese goods, manufacturers face another wave of trade uncertainty. It’s clear that strategies reliant solely on stockpiling are insufficient to address the long-term complexities of a tariff-driven trade environment.
The last trade war revealed several critical drawbacks of stockpiling: